ITER is the world’s largest fusion power experiment and if it can overcome some immense technical challenges, it’s no exaggeration to say that its success will change the world.
The dream of fusion power depends first and foremost on a self-sustaining fusion reaction, with most of the heating power needed coming from within the reaction itself, rather than from external sources. This is what ITER is all about: trying to create those conditions, in a stable and predictable way, as a starting point towards developing future fusion power stations.
We are the lead organization in the MOMENTUM joint venture, the project’s construction management-as-agent (CMA) contractor, which is responsible for coordinating the assembly of more than one million components in the ITER machine. The CMA task began in 2016 but our support to the 35-nation initiative, based in Provence, France, goes back decades.
Amentum’s contribution to ITER includes the first wall panels which protect the machine from plasma temperatures of up to 150million°C; the test blanket modules, which are an essential part of breeding tritium to fuel the fusion reaction in future reactors; and the remote handling system for maintaining the neutral beams, which heat the reactor’s fuel.
Three heating neutral beam (HNB) injectors heat the plasma by firing a stream of neutral (un-charged) particles into it at a tangent. Exposure to radiation means that the HNB machines will become highly activated, so internal maintenance and repairs will need to be carried out remotely.
We led the European Remote Handling Alliance, a co-operative group of companies responsible for the design, manufacture, installation and commissioning of the Neutral Beam Remote Handling System which will connect/disconnect components weighing up to 40 tonnes (44 tons) and transport them out of the cell to a separate facility.
Design development work, technical specifications and implementation plans for ITER’s integrated plant simulator have also been entrusted to us and three sub-contractors: the UK Atomic Energy Authority, Fortum and VTT Technical Research Centre of Finland Ltd.
To validate the design and design modifications, plant simulators are being developed for the heating, plasma and cryogenic systems. The integrated plant simulator is vital in understanding the behavior of the full ITER machine because it provides the capability to simulate how these interconnected systems interact. It will also bring an integrated approach to the training of operators and will support the commissioning and operation phases at ITER.
We carried out design and engineering work on remote handling tools for maintaining the stainless steel plus that will seal off the ports on the Tokamak and Hot Cell Complex. Thirty plugs, weighing up to 48 metric tons and designed to be removed for maintenance, are essential for the complex task of carrying and protecting some of the precious payloads of the machine, including diagnostics and heating system elements that are critical to efficient operation.
Our specialists assisted the ITER procurement process by helping to finalize the specifications and invitation to tender (ITT) process for the Detritiation Plant, which will remove tritium from the HVAC system in normal and accident conditions to ensure that any air discharged is compliant with regulatory requirements. We provided industrial learning-from-experience during the preparation of the ITT package.
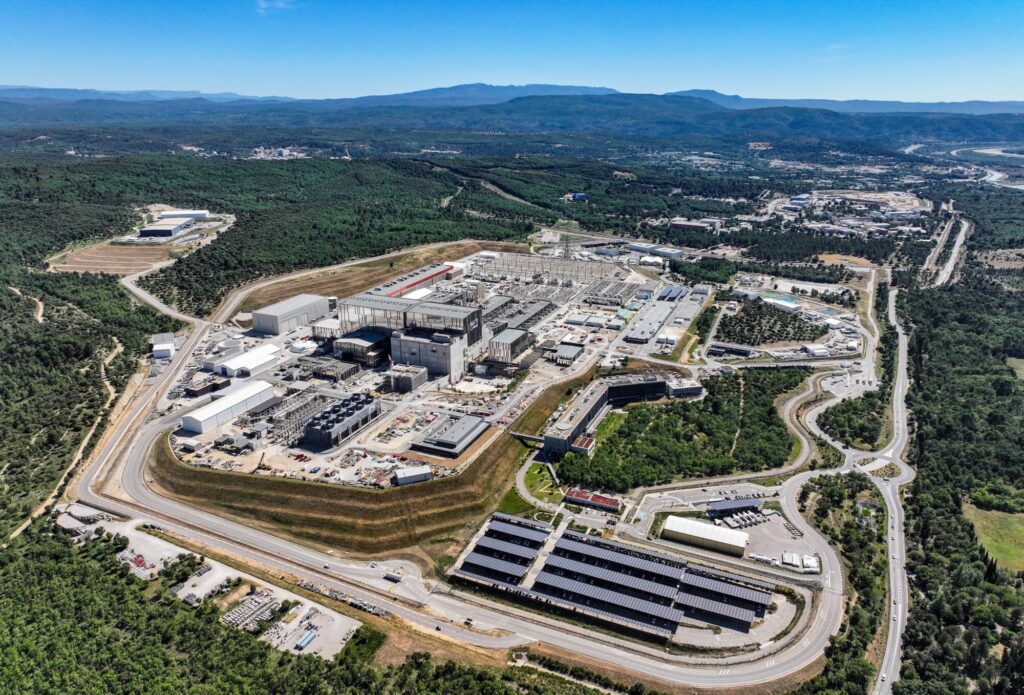