Robotics Design and Development for Harsh Environments
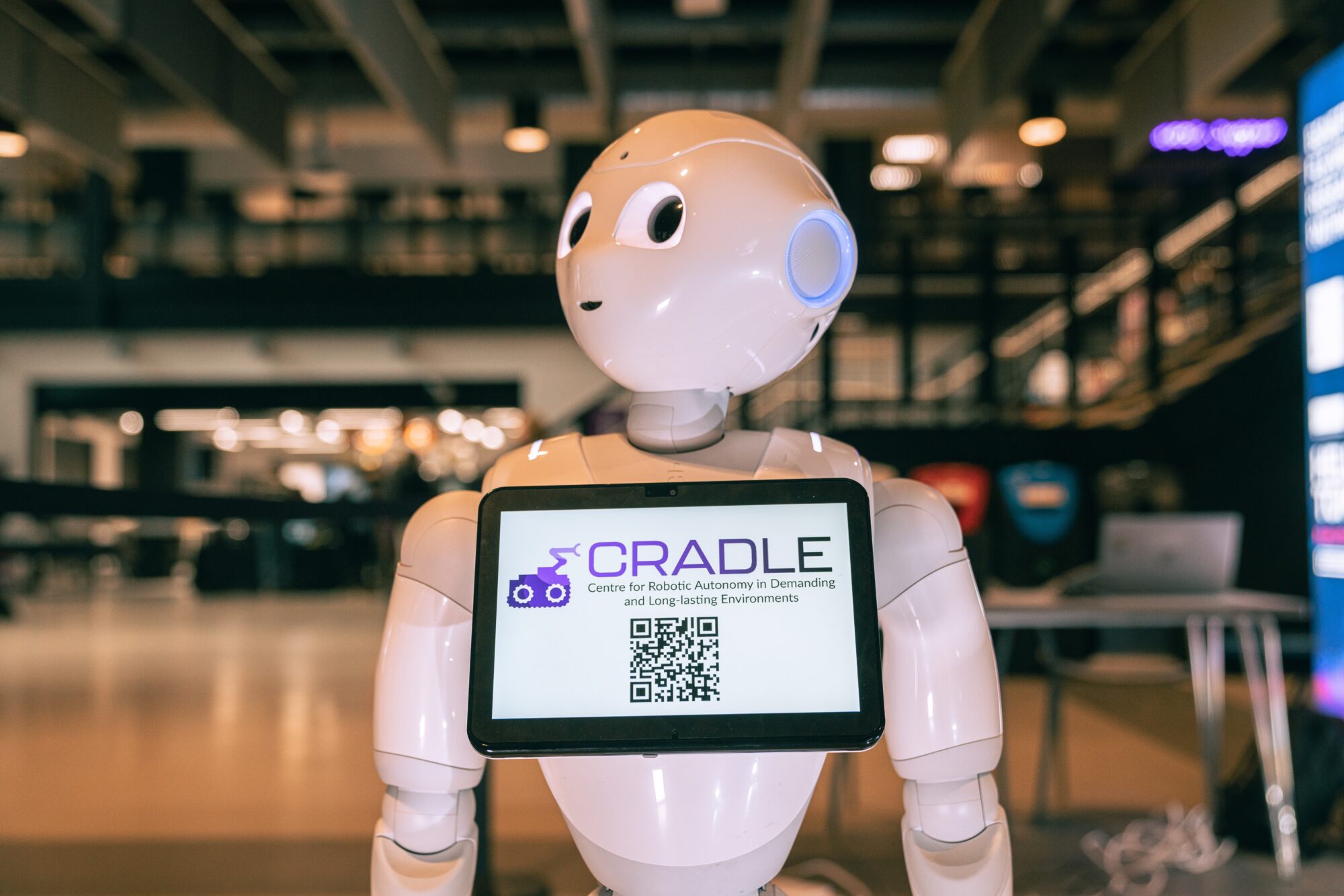
Amentum’s expertise in robotics was born in the harshest environment possible – the interior of nuclear reactors. The skills we have developed are now being used to gather data to inform how we can extend the life of infrastructure from roads to waterways and energy networks.
When a rise in temperature was detected inside reactors at the Heysham 1 and Hartlepool nuclear power stations in 2006, it was the cue for robots to show what they can do. Excessive heat in the hot box domes – steel structures which separate gases at different pressures – meant that output had to be reduced to 75% of full load, leading to loss of revenue. Carbon deposition was to blame and to restore cooling, a series of new bleed holes needed to be created deep inside the reactor.
We worked with EDF to develop a strategy to create additional bleed holes using three bespoke, robotic tool packages. These were deployed through some of the reactor’s standpipes, enabling operators to detect the correct height, drill through the standpipe and create the bleed hole in the surrounding nozzle, and then weld a plug into the initial hole to restore the correct gas flow. The solution was successfully deployed on site only six months from project start, and all four reactors were able to return to full power.
Without robots, it’s impossible to implement major engineering change in an environment too hazardous to allow human access. The Hot Box Dome project was groundbreaking at the time, but advances in sensor technology, data analytics and artificial intelligence mean that robots can now make an even bigger difference to nuclear operations and decommissioning.
For the Nuclear Decommissioning Authority’s Integrated Innovation for Nuclear Decommissioning competition in 2017, Amentum and nine collaborating organisations developed a prototype of an end-to-end nuclear decommissioning system designed for post-operational clean out of disused reprocessing cells at Sellafield. The system enabled on-site characterisation by bringing the laboratory into the cell using a remotely operated tracked vehicle which carried sensors and robotic tools to collect and transmit data for analysis. A robotic laser cutting system was developed for dismantling of equipment inside the cell.
Amentum is moving fast in the growth area of remote inspection – where robots gather data in situations where humans would find it impossible or hazardous to enter. Going beyond the nuclear industry, we are developing systems to inspect sewers, pipelines, storage tanks, river beds and transportation networks.
We have designed and built a submersible robot which is being used by the British Army to remotely survey the best location for installing pontoon bridges across rivers and other obstacles.
To take research to the next level, Amentum and The University of Manchester are leading the Centre for Robotic Autonomy in Demanding and Long-lasting Environments (CRADLE). It was set up under the Engineering Physical Sciences Research Council’s Prosperity Partnership programme, which seeks to enable business and academia to harness new technologies and apply them more quickly and effectively.
PhD researchers from CRADLE work at the university and at Amentum’s laboratories in Birchwood Park, Warrington, to develop more reliable components and sub-systems for robotic devices, more resilient and verifiable software architectures, and demonstrators of next generation solutions. The human factors and ethical aspects of robotics are also an important part of CRADLE’s remit.
Amentun’s Engineering Development Director, Duncan Steel, who serves as CRADLE Industry Director, adds: “The reasons for launching CRADLE are to progress fundamental research capability at the cutting edge of robotics, but also to deliver impact by commercialising innovation and ensuring that it meets the real needs of industry. Also important to me is that CRADLE will develop skills and talent, ensuring a pipeline of world-class people in the robotics field and supporting further growth in both organisations. Autonomous inspection and repair systems increase our capability to extend the life of water and energy networks, roads, bridges and railways, which makes infrastructure more sustainable, reduces the need for new build and advances the shift to a net-zero carbon economy.”